CMP, also known as
Chemical Mechanical
Planarization, is a
polishing process
combining mechanical
friction and
chemical etching. It
is used to achieve
surface planarity in
the nanometer
range, on components
such as
semiconductor
substrates or
wafers for the
electronics
industries.
Some years ago, the
CMP process also
revolutionized the
production of
ceramic and sapphire
components, such as
sapphire watch
crystals,
substrates, windows
and lenses. The CMP
process allows all
traces of mechanical
diamond polishing to
be removed. However,
it remains
relatively
expensive and
therefore forms a
significant part of
component cost. The
advent of nanometre
size micron diamond
powders created
prospects for
significant
improvements in
productivity and
cost savings.
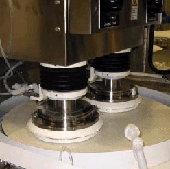 |
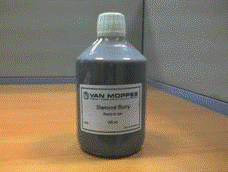 |
CMP-Chemical
Mechanical
Polishing |
CMP DP
slurry |
CMP-VM125
mainly consists of
colloidal diamond
powder in a
deionised water
base. It is
guaranteed to be
exempt of
agglomerates and is
chemically neutral.
It can be mixed with
any CMP slurry
formulation. A 250g
bottle is enough to
boost the
productivity of a 10
litre CMP slurry
supply. It mixes
easily and remains
in perfect
suspension through
the slurry
recirculation
movement.
CMP-VM125
requires no change
in your established
CMP process. The
benefits, however,
are considerable.
Here is the proven
advantage that was
demonstrated in
several sapphire
watch crystal
manufacturing
locations:
up to
50% reduction in
polishing time
which potentially
results in
-
50% reduction in
machine and
operator time
-
50% reduction in
CMP slurry
consumption and
slurry disposal
cost
-
50% reduction in
polishing pad
consumption
-
100% increase in
output per
machine and time
unit
-
Improved
component
surface geometry
-
Reduced reject
rates
If
required, the
standard CMP-VM125
formulation may be
further adapted to
suit your exact CMP
application
requirements.
|